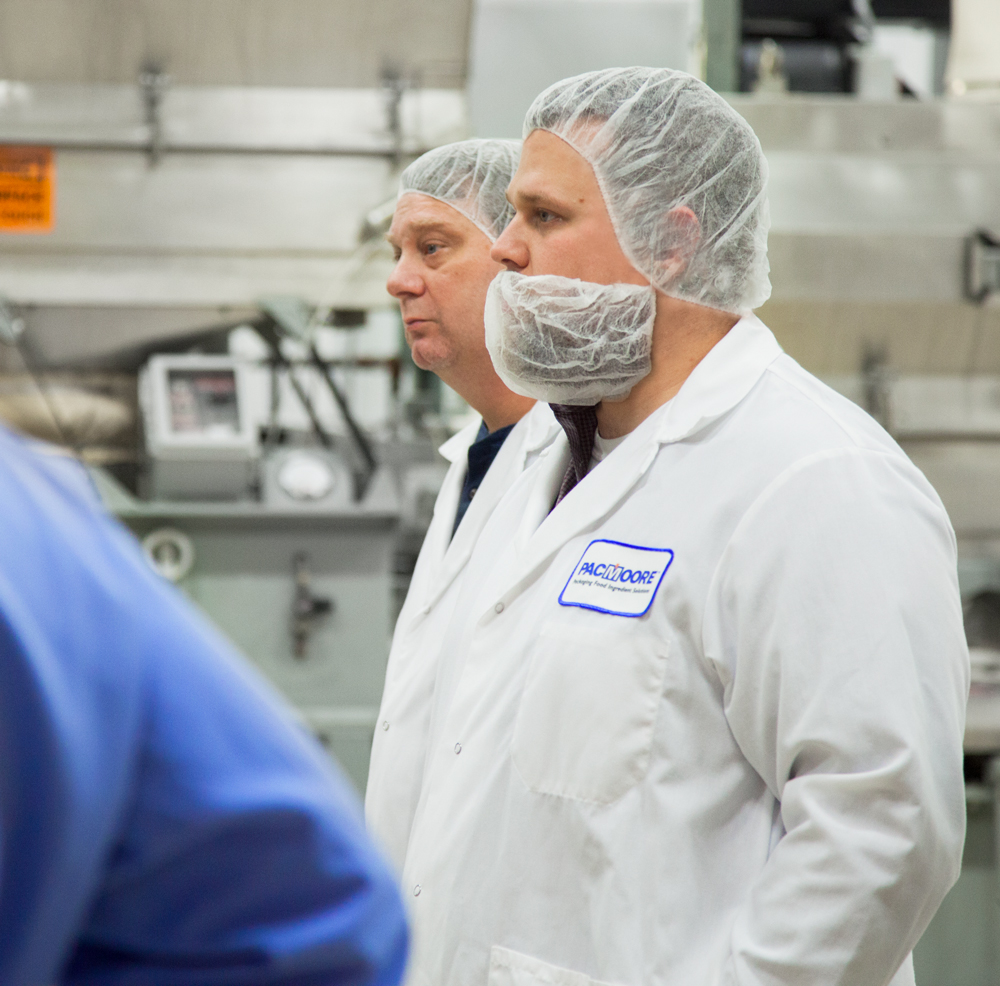
I joined PacMoore in November of 2016 as Extrusion Engineer during the last phases of system installation. Since then, I’ve been managing the extrusion projects on our full scale system as well as developing and training enthusiastic employees over new equipment and policies at our plant in Mooresville. In these short seven months we’ve been able to streamline our processes and successfully navigate the intricacies of a dynamic food processing system. This has been made possible by a multitude of individuals; especially the leadership and hard work of Operations Supervisor Chuck Frye and other eager supporting staff.
Efficient and Versatile Extrusion Systems
Our pilot and full-scale extrusion systems both utilize twin screw extrusion technology. This makes scaling up projects from the development phase to the production phase very simple. Twin screw extruders are much more versatile than their single screw counterparts, allowing for higher fat and water content in the formulation if needed. The entire system is complimented with our preconditioner, conveyor dryer, classification equipment, metal detection and magnets. After the extruded products are cooled, they are packaged at a station conveniently located at the end of the conveyor dryer for maximum efficiency. From Gaylord totes to bulk bags to bags-in-boxes, practically any packaging necessary can be accommodated.
Customization of the Products we Create
Product customization is truly built in to our system, thanks to the interchangeable dies and other adjustable features of our system. Nearly limitless options exist for product shape and formulation. Added protein is trending right now, so we’ve made extruded crisps, bits, and pieces with up to 60% protein content – and we can go even higher. Depending on the density and other factors of each particular product we’re running, the rate of production can reach as high as 3,000 lbs. per hour.
Are you looking for experienced extrusion partners? Our production schedule is filling up fast, but we’re ready to work with you! Contact us today so that we can accommodate your extrusion project.